Investment Casting Handmade Jewelry
Anatomy of the Lost Wax Casting process
Setting The Sprue
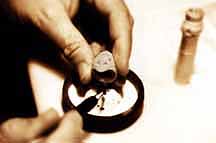
Placing the wax ring on a sprue
In casting, a sprue is the passage through which a molten material is introduced into a mold, and the term also refers to the excess material which solidifies in the sprue passage. In sand casting, the sprue is formed by a dowel which is removed from the sand to make the hole into which the metal is poured.
Sprues can serve as filters, heat sinks, and as feeders. Bronze in particular has a high shrinkage rate as it is cooling; a sprue can continue to provide molten metal to the casting, provided it is large enough to retain its heat and stay liquid, as metal in the main casting cools and shrinks. The design of the sprue and runner system can be also utilized to trap unwanted dross and sand from continuing into the main cavity; this may include adding porous material to the runners, or designing the sprue to eject the dross to the side of the sprue using cyclonic separation.
Making An Investment
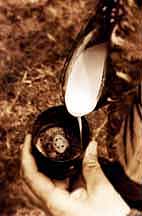
Plaster investment is mixed and poured into the flask, covering the wax
The sprued wax pattern is dipped into a slurry of fine refractory material, known as investment material; one example of this is silica. This fine material is used first to give a smooth surface finish and reproduce fine details. During the primary coat(s), the sand will typically be a zircon-based, as zirconium is less likely to react with the molten metal when poured into the shell. The cluster is then dipped into a fluidized bed, rain tower sander, or by hand into a sand-like stucco, which is dry crystalline silica of a controlled grain size, and allowed to dry. These secondary coats usually are mullite, molochite, chamotte, or fused silica refractory material. This step is repeated until the investment is the required thickness, which is usually 5 to 15 mm (0.2 to 0.6 in).
As an alternative to multiple dips the cluster is placed upside-down in a casting flask and then liquid investment material is poured into the flask. The flask is then vibrated to allow entrapped air to escape and help the investment material fill in all of the details. Prior to silica, a mixture of plaster and fire-proof material such as chamotte was used. An alternative to using silica is a slurry of ethyl silicate (alcohol-based and chemically set), colloidal silica (water-based, also known as silica sol, set by drying) or a hybrid of these controlled for pH and viscosity.
Melting
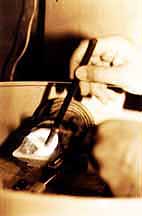
Metal casting grain is melted prior to injection by a centrifugal caster
The investment is allowed to completely dry, which can take 24 to 48 hours. It is then turned upside-down and placed in an oven to melt out or vaporized the wax. The melted wax can be recovered and reused, although often it is simply burned up, this is called burnout. At this point metal casting grain of the desired ring material is melted for pouring.
Spinning
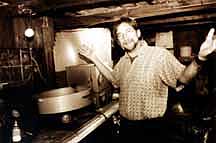
Molten metal is spun into the hot flask, replacing the wax removed during burnout
The molten metal is then poured into the mold by a centrifugal caster. A centrifugal caster is used as a means of casting small, detailed parts or jewelry. An articulated arm is free to spin around a vertical axle, which is driven by an electric motor or a spring. The entire mechanism is enclosed in a tub or drum to contain hot metal should the mold break or an excess of metal be used. A small amount of metal in a crucible (a sort of ceramic pan) next to the mold is heated with a torch. When the metal is molten the arm is released, forcing (by centrifugal force) the metal into the mold. The high forces imposed on the metal overcome the viscosity, resulting in a finely detailed workpiece. A similar advantage is obtained by vacuum casting.
Quenching The Flask
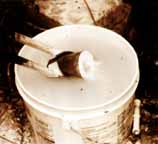
The investment is removed and the flask is cooled
The flask is cooled and the investment material is blasted or chipped off.
The Result
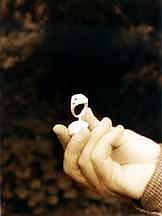
This sprue button and attached ring are now ready for polishing
The ring is now ready to be prepped for sale. The ring is polished and buffed and removed from the Sprue.